|
Newsroom >
Business
>
Business
>
Priest Electric Explains How To Reduce Electric Motor Bearing Failures
Priest Electric Explains How To Reduce Electric Motor Bearing Failures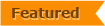
There are several reasons to do an electric motor rebuild, but the most common is bearing failure. It has been suggested that as much as 80% of all the electric motor rebuilds are done because of a bearing failure.
Caldwell,
ID,
United States of America
(sardnews.org)
30/07/2013
There are several reasons to do an electric motor rebuild, but the most common is bearing failure. It has been suggested that as much as 80% of all the electric motor rebuilds are done because of a bearing failure. These failures can be due to improper bearing use, improper maintenance or improper installation of the electric motor. Proper installation and maintenance of bearings can result in a much longer useful life for any electric motor.
The most crucial factor in avoiding early bearing failure is an optimal operating environment. In a perfect world, the bearing environment would have a low humidity, be contaminant free, have no vibration, and have a consistent temperature. The bearing loads would be perfectly balanced, and there would be continual lubrication to combat friction and bearing wear. In an environment such as this, bearings could be in constant use and last indefinitely. In reality though, we know that no electric motor operates in these conditions. While we can only dream of the perfect environment for bearing use, we can certainly do some things to make the environment as satisfactory as possible.
The first step you can take is to align the motor shafts properly when the motor is installed. Any misalignment between the electric motor shaft and the driven equipment shaft can cause a premature failure of the motor bearings. The reason is that misalignment will cause excessive loads and vibration. We already know that we want to eliminate vibration and minimize the bearing loads whenever possible.
While couplings are flexible to reduce the effects of misalignment, it is never a smart idea to take advantage of the coupling flexibility. Instead, secure the driven motor parts and then install the coupling.
Next we move on to the problem of moisture. While you may not be able to control the level of humidity and moisture, you can certainly manage it to minimize the effect it has on bearing life. In most cases, humidity will have little effect on running motors. It is only once the motor is turned off and allowed to cool down that condensation forms. This is something you can manage. Take steps to guard against the condensation such as using a grease that is fortified with rust inhibitors and rotating the shaft of the idle motor on a frequent basis. Another option is to install heaters in the motor.
Next, you should take whatever steps necessary to minimize vibration of the motor. Vibration is one of the major causes of bearing wear, which will ultimately lead to bearing failure. Make sure the equipment being driven is in balance, or has been balanced. This could include fans, impellers, or other rotating parts.
While there are other steps you can take to maximize the life of motor bearings, the ones above are the most critical if you want to extend the life of the motor and avoid frequent electric motor rebuild situations. In the case of electric motors, it is unquestionably true that an ounce of prevention is worth a pound of cure.
For more details visit: http://www.priestelectric.com/
###
About Priest Electric
Started over 50 years ago, Priest Electric is a Boise based electric motor repair company. They also operate in Idaho, Nevada, and Oregon. To know more, visit, http://www.priestelectric.com/
|